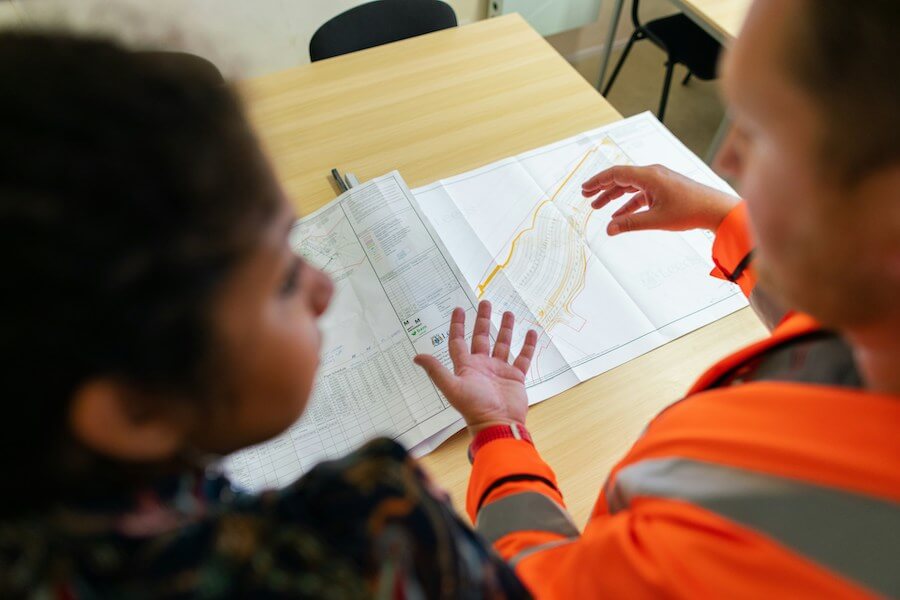
FMECAs (Failure Modes, Effects, and Criticality Analysis) are crucial in crafting effective maintenance strategies, serving as a cornerstone in preventing unplanned downtime. A key element in this strategy development is the facilitation of a review workshop focused on identifying failure modes, assessing their effects, and evaluating associated risks. This process entails initially analysing the impact of failure without any preventative tasks, followed by a revaluation with preventative measures in place.
This is often perceived as a dauting task due to the perceived time and resource requirements. However, its benefits often far outweigh the initial investment of time and resources. By properly implementing an FMECA based maintenance strategy, organisations can significantly improve asset reliability, reduce downtime, and optimise maintenance costs in the long run.
SME involvement in the FMECA facilitation process brings expertise and ownership into the maintenance strategy.
When facilitating a FMECA, the “dream team” consists of various SMEs from the maintenance team, who each give their input into the draft FMECA document.
The ideal FMECA facilitation team could include 1 – 2 people from each of the following positions:
- Mechanical Tradesperson
- Electrical Tradesperson
- Asset Operator
- Maintenance Planner
- Reliability Engineers/Managers
- Original Equipment Manufacturer (OEM) Representative
And of course, a skilled FMECA Facilitator.
While going through the draft version of the FMECA, each of these stakeholders has the opportunity to ask questions, provide their expertise, make suggestions and discuss their opinion of the strategy at hand.
This results in two things;
1. A technically accurate and comprehensive strategy.
By involving each of these SMEs, they are bringing with them a wealth of knowledge to the facilitation. The OEM representative (engage one of their service technicians) is a knowledge hub for the equipment, which in the specific example of a recent client was essential to the process, as the asset was brand new to their organisation.
2. A sense of ownership over the FMECA components and corresponding maintenance strategy
By involving the personnel who are responsible for carrying out the maintenance in the FMECA facilitation, you are inviting them to have input over processes that they will carry out on a daily, weekly and monthly basis. Not only are they able to provide expertise on whether or not the maintenance action suggested is plausible or physically possible, but they also will feel involved and connected to the maintenance strategy.
We often receive feedback from management in mining organisations such as our recent client, where they report that maintenance task completion rates and quality of the preventative maintenance tasks performed increases after their maintenance personnel are involved in the FMECA facilitation. This is because they contributed to the strategy creation, and it becomes more than a simple ‘tick and flick’ to do list generated at the start of their workday.
Comprehensive Asset Failure Understanding: Facilitation Workshop for Internal Stakeholders.
The facilitation workshop provides internal stakeholders with a thorough understanding of potential issues and the mechanisms of asset failure. During a FMECA session and the detailed review of the analysis, participants develop a profound comprehension of how each asset component interacts and how a single component failure can impact the entire subsystem or operation. This deeper insight into failure effects enables stakeholders to make strategic decisions that can be integrated into the overarching maintenance strategy and corresponding work orders.
It provides an open forum to review and validate the strategy and customise it according to organisational needs.
The process of workshopping the FMECA in detail with internal SMEs, any errors or overlooked items are bought up, discussed and then actioned accordingly. This ensures that from every perspective (electrical, mechanical, OEM, planning) the maintenance strategy is sound and error-free.
You could have one of the most knowledgeable and experienced Reliability Engineers in the world complete an in-depth FMECA, and base it off of highly detailed OEM documentation, but if they don’t facilitate the workshop with the right SMEs involved, your maintenance strategy will still be insufficient.
There really is no substitute for engaging SMEs within your organisation to review and validate the FMECA document. Just because a maintenance task is suggested to be completed in a certain manner by the OEM or historically done that way, doesn’t mean that it will work in practice for your organisation and the current operating environment. The best maintenance strategies are the ones that are able to be implemented, followed and each task is adding value to the equipment reliability – and discussing the FMECA, work orders and work instructions with your internal team is the best way to achieve this.
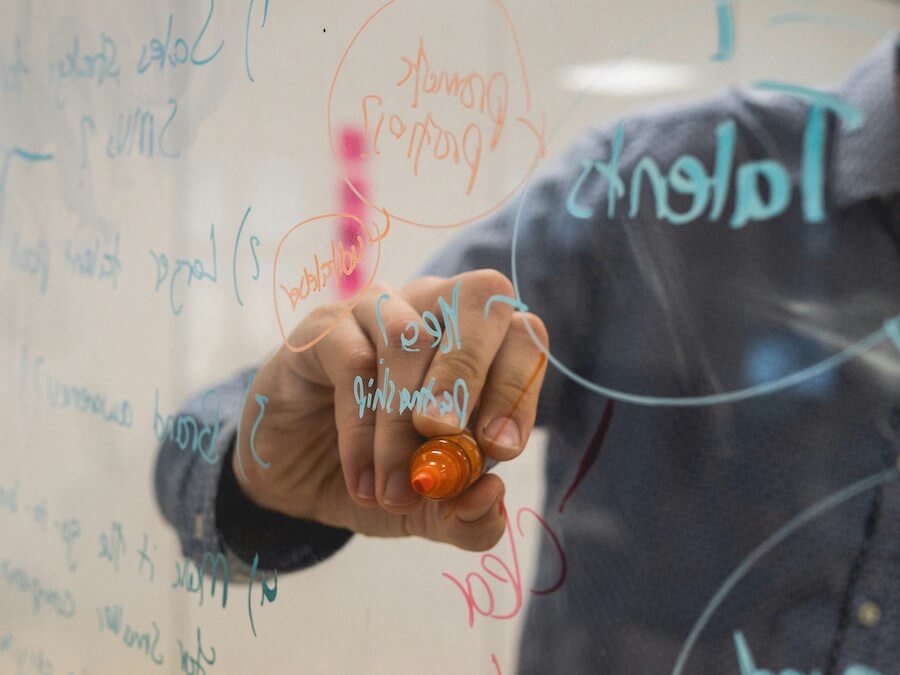
It allows stakeholders to make informed decisions, while incorporating input from other SMEs in the room.
During the facilitation process, the key stakeholders discuss all of the ways in which the asset in question can fail. Then, they discuss the potential causes of failure and the associated maintenance tasks required to ensure those failure modes don’t occur. The risk of conducting (or not conducting) said maintenance tasks is then weighed up against the organisational risk matrix.
During this entire discussion, all stakeholders from the operators, to tradespeople, to planners get to provide input, voice concerns and provide reasoning for decisions being made. This allows the entire team of stakeholders to gain a common understanding of the asset maintenance strategy being developed and consequently make decisions according to organisational goals.
In summary, the benefits of an FMECA facilitation workshop are multifold. This process is instrumental in establishing effective maintenance strategies that enhance asset reliability, minimise downtime, and optimise maintenance costs. It allows for the involvement of Subject Matter Experts (SMEs)—including mechanics, electricians, asset operators, maintenance planners, reliability engineers, and OEM representatives—who collectively review, refine, and approve the maintenance strategy.
This collaborative approach not only ensures the technical accuracy of the strategy but also fosters a sense of ownership among the implementers. Moreover, it empowers all stakeholders to gain a deeper understanding of potential asset failure issues, enabling them to make strategic decisions in line with organisational goals. Finally, the FMECA workshop provides a platform for stakeholders to identify and correct any errors or overlooked aspects in the maintenance strategy, reinforcing its robustness and effectiveness.