Caterpillar Dozer Final Drive Root Cause Analysis
Industry: Mining Sector
Services Required: Root Cause Analysis, Condition Monitoring
Location: Australia
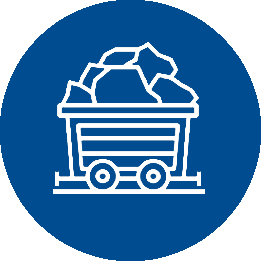
A specialist mechanical engineer with significant OEM-engineering experience was assigned to conduct the investigation. into the performance of Caterpillar dozer final drives.
The engineer conducted off-site analysis on the oil sampling records, and coupled with their extensive equipment knowledge, concluded the root cause of abnormal samples was transmission oil mixing with final drive oil.
In conjunction, the laboratory alarm limits were recalculated using current site sample data to provide earlier warning of internal contamination and therefore component degradation.
THE CHALLENGE
Large counts of “abnormal” samples were evident in the clients extensive corporate oil analysis database. A significant contributor was the final drives in a specific make and model of tractor across their multiple operations. The root cause of the disproportionate count of abnormal samples was required.
THE SOLUTION
The engineer commenced exploratory data analysis and quickly determined the abnormal samples were predominately flagged for “high wear” or “oil” problem codes.
Further analysis showed the “wear” samples did not suffer from dirt ingress (indicated by silicon and aluminium); instead, iron was being generated internally in the final drive.
The “oil” samples were generally flagged due to low viscosity. Plotting viscosity and iron on the same chart showed a correlation – as viscosity decreased, iron increased. This would be as expected if the thinner oil film is unable to support operating loads.
Analysis of the oil additive pack at these same times suggested the final drive additive pack was consistent with transmission oil. Either the compartment was being filled with the wrong oil, or oil transfer was occurring between the compartments. Site investigation concluded incorrect oil fill was unlikely, thus oil transfer past the axle oil seal was considered the most likely culprit.
The oil sampling limits were considered wide, and closing the limits would provide the site more warning of abnormal internal conditions in the final drive. The limits were recalculated according to ASTM D7720-11. This involves setting the triggers at the 95%, 98% and 99% values of the cumulative distribution function.
THE RESULTS
The specialist engineer was able to identify the root cause of the abnormal samples, provide guidance as to the fix and recalculate improved oil sample limits for the client.
“The engineers wealth of experience and OEM knowledge ensured the root cause was identified by following a systematic process”
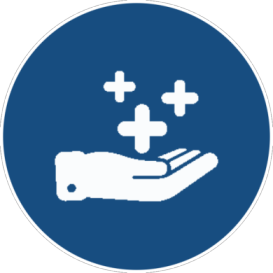
Added Value
The analysis created value for the client by:
- Accurately identifying root cause of abnormal oil sample results
- Focusing attention on maintaining oil viscosity and film strength to maintain compartment cleanliness and maximise component life.
- Using more rigorous oil sample analysis limits to ensure the site analysts were able to identify the same root cause in the future
HolisticAM was able to deliver this value with engineers that have 20-years experience with equipment OEMs and significant site operational experience.
Need Help?
If you want to know more about this project or would like to discuss anything relating to Maintenance Management, don’t hesitate to talk to us!