Service
Predictive Maintenance
We help your organisations embark on a predictive maintenance regime which reduces the likelihood of failures, increases reliability by avoiding costly downtimes, reduces the cost of ownership by lowering maintenance costs, and improves business reputation through optimising its supply chain.
What is Predictive Maintenance?
Predictive maintenance (PdM) is a methodology that considers the state of a business assets or equipment and estimates their time-to-failure. It continuously monitors assets and equipment based on the analysis of data collected under varying operating conditions in order to anticipate problems that lead to failure.
Once the predicted failure time is known, the optimum time to schedule maintenance for the assets can be calculated. Predictive maintenance ultimately prescribes the most efficient corrective action by applying advanced analytic techniques on big data including technical condition, usage, environment, maintenance history, similar equipment elsewhere and, more generally, anything related to the performance of assets and equipment.
With substantial and continuous capital investment in the fields of predictive analytics and condition monitoring systems and equipment, what these technologies can offer to maintenance planning and optimisation keeps on growing. Companies are doing much more to increase the maturity of their maintenance and laying the foundations for such maturity increases. Those who have implemented Predictive Maintenance regimes have reported improvements in one or, in most cases, several key maintenance value drivers such as uptime, risk and lifetime of their assets.
Does your business have any of the following traits?
- Have very high operational expenditure (OPEX) and capital expenditure (CAPEX)
- Have tightly integrated supply chains where any reduction in efficiency results in substantial disruption to the supply chain
- Have very sensitive, complex and expensive assets or machinery
- Have assets or equipment that pose high risks to safety and cause health and environmental hazards in case of failure
- Have assets or equipment that fail unexpectedly or regularly
- Frequently faced with increased downtime due to failures and a lack of stock of spare parts
- Equipment condition deteriorates quickly due to exposure to harsh conditions
If any of these traits sound familiar, you will find Predictive Maintenance and its benefits of particular interest and critical to your operations.
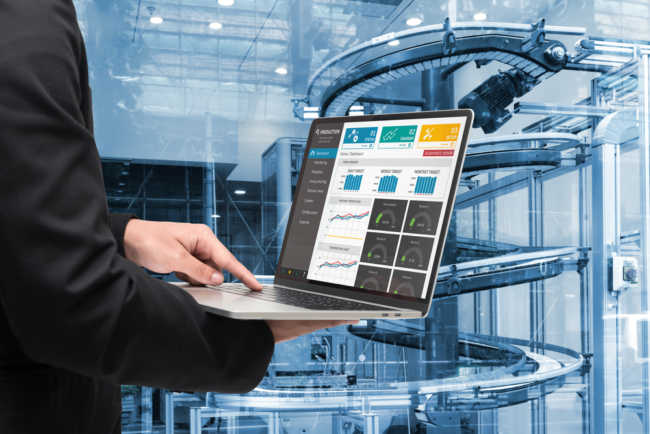
How is our Predictive Maintenance service achieved in your organisation?
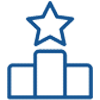
Step 1: Feasibility Study and Asset Criticality Ranking
Only highly-critical and moderately-critical assets are worthwhile and feasible to be included in Predictive Maintenance to increase their reliability. Assets for which sufficient data can not be obtained are not good candidates for Predictive Maintenance. A feasibility study should be conducted to establish the business case for Predictive Maintenance implementation.
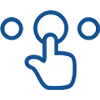
Step 2: Asset Selection
Instead of addressing the entire asset classes, those that can be included in a pilot plan should be selected first. Once the necessary lessons are learnt, Predictive Maintenance can be rolled out to other classes of assets within the business.
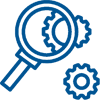
Step 3: Reliability Analysis
Perform the root cause analysis (RCA) and the failure mode and effects analysis (FMEA) on each asset class to gain insight about:
- Data required to monitor root cause and failure modes;
- Required measurements and external data;
- Interrelation of root causes and failure modes.
It is the first step in the Predictive Maintenance development process where reliability engineers and predictive analytics specialists need to work together.
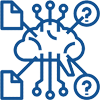
Step 4: Predictive Maintenance Methodology Design
The success of a Predictive Maintenance system lies in this step where predictive analytic techniques and algorithms are chosen. The quality of predictions is heavily dependent on these models. Having a solid reliability model developed in step 3 is crucial for the design of a fully functional Predictive Maintenance methodology.
Machine learning algorithms are particularly crucial for optimisation of Predictive Maintenance algorithms. They are used to detect anomalies and different types of faults through classification as well as predicting the transition from a healthy state to failure (remaining useful life, RUL).
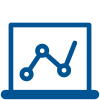
Step 5: Real-time Condition Monitoring
This is where the designed Predictive Maintenance methodology is in action processing data from various sources, monitoring and visualising the performance of the selected assets in real-time.
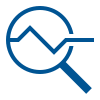
Step 6: Failure Prediction
Data from various sources such as sensors, condition monitoring systems, maintenance and failure history or third-party providers are used to predict future failures. Initially these predictions can run alongside existing routine maintenance procedures instead of taking maintenance actions solely based on Predictive Maintenance predictions until confidence is built on the developed a Predictive Maintenance methodology.
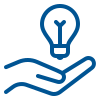
Step 7: Recommendation of Corrective Actions
A thorough Predictive Maintenance methodology should be able to recommend the best action for avoiding a failure based on a set of standard maintenance types and tasks. It may also be able to execute such tasks by issuing the corresponding work orders automatically.
We are ready to help!
We have extensive experience in predictive maintenance to help your organisation make better decisions. If you want to discuss your projects or need any help, don’t hesitate to talk to us!
Why You Should Choose HolisticAM for Predictive Maintenance Service?
Predict the unpredictable
HolisticAM tackles the unforeseeable and inexplicable failures with big data and predictive analytics. It harnesses the power of artificial intelligence to create insights and detect patterns and anomalies that escape detection by routine maintenance activities.
Turn predicted failures into analytic successes
Predictive maintenance is done right at HolisticAM. We believe the analyses are not only a means to a predictive end but also a means of analytical insight and discovery. We analyse what needs to be analysed and predict what really needs to be predicted to provide statistically meaningful answers to your organisation.
Implement Predictive Maintenance successfully with management support
HolisticAM with its proven management support experience is best positioned to help you reap the full rewards of Predictive Maintenance by ensuring that all management and planning systems are in place to enable your Predictive maintenance objectives to be realised.
Generate sample failure data
If your organisation lacks the failure data for accurate results, HolisticAM will help you to stop this from becoming a fatal deficiency by generating sample failure data for you with the right tools. Physical models of the asset are developed, and a variety of failure scenarios are incorporated into the models. These scenarios can then be simulated, and the resulting failure data is labelled and stored for further analysis.